Interesting fact! The shape of a new shoe depends on the shape of the hoof. Every year fashion trends bring many new styles and shapes to shoe manufacturing.
- The variety of lasts (shoe shapes)
- 19 Replies to 'Different Types of Shoe Insoles (Shapers)'
- Manufacture of shoe inserts
- How to make a shoe block at home
- #4 OFFLINE LeLab
- #5 OFFLINE yaso73
- Prefabricated hooves and custom-made ones
- What do the shoe lasts look like?
- Last pattern of shoes
- APPLICATION OF LASTS
- Technical requirements for shoe lasts
- The evolution of the hoof: How technology has changed over the last hundred years
- What are good lasts for shoes useful for?
- –Keywords
- Unattainable ideals
- Work with pads, pay with pads
The variety of lasts (shoe shapes)
If you decide to buy good and expensive shoes, you should consider purchasing special lasts, sometimes called 'shoe spacers' or 'shoe molds'. The English use the simple but somewhat imprecise term shoe trees, which literally means 'shoe trees'.
Surprisingly, there are many types of shoe trees - and that's why I decided to write a long article giving an overview of them. I would like to emphasize once again that these are accessories and not the lasts onto which the shoes are sewn.
This is the cheapest option. You are most likely to find these spacers in multi-brand discount shoe stores, as well as small shops and kiosks that sell shoe cosmetics. Sometimes they cost less than 100 rubles (at IKEA – only 59 rubles!); the most expensive - the Saphir brand - are made in France and cost about 600-650 rubles.
But even the French plastic partitions are a bad choice, a classic example of the 'cheap and serdito' series. Unlike wood, plastic cannot absorb odors, absorb moisture and do not help dry shoes.
And the partitions as such have another disadvantage. They are not inserted completely into the shoe like full-fledged insoles, but are curved. The end, which is connected to the front of the spacers by a thick metal spring, must be bent and inserted directly into the 'heel' of the shoe. This naturally puts pressure on the heel area and the back of the shoe and the back of the insole can deform over time.
This is a better option than plastic spacers, but worse than full wooden inserts. Wood absorbs moisture and eliminates odors, which is a good thing. However, the flaw in the spacers described above remains. Of course, you can simply push the spacers into the shoe without retracting the toe, but then the wrinkles will not be smoothed out, but the shoe will generally feel good - thanks to the properties of the wood already described.
19 Replies to 'Different Types of Shoe Insoles (Shapers)'
I use cheap plastic shoe insoles wrapped in paper. The paper absorbs moisture and odors and is very hygienic it seems.
Have you ever worn satin shoes? I like sneakers http://www.adidas.ru/krossovki-zx-flux/B34485.html But the satin upper is alien to me. Do they last long?
1 Thank you for your website. She is very informative.
2 – I have always bought Woodlore shoes. They are optimal in terms of the price/performance ratio. But now it is difficult to buy them in Moscow, they are American. Avel are decent budget pads, but they have an odd size range. My husband is a size 42.5 and the 42-43 insoles are hopelessly small. The 44-45 insoles fit a size 44 shoe, but I like my shoes to fit closer to the insole. With the size selection of 40-41, 42-43, 44-45 I can't fit my husband. He's not too keen on buying insoles more expensive than 3k for 10-15k shoes (that's what we buy, or cheaper if there are discounts). We would love to buy the insoles with the shoes, but the offline stores don't have them in the mid-price segment.
I would like to add that in addition to wooden and plastic molds, there is also a very good and not so expensive alternative - foam molds with an antibacterial substance. They are available with both stems and springs and in various shapes - especially for boats, comforters, ballerinas... Take a look at the NICO Germany brand.
Dimitri, tell me. What about winter boots with fur? Because the idea is that the insoles, which are constantly in the shoes, put pressure on the fur.
In Western Europe people rarely wear boots with fur…. Personally, I only put insoles in my winter boots at regular intervals, and I haven't noticed that they ruin the fur - but when you have boots on, your feet also put pressure on the fur - so it changes with it, so to speak, even without insoles over time and is generally hardly broken down. Aside from that, interacting with cedar wood is also good for fur – it minimizes odors and removes excess moisture.
When I put my winter boots away for the winter, I fill them with crumpled paper or newspapers without any noticeable smell. By the way, this is the cheapest alternative to insoles, even if it's not exactly full-featured.
Manufacture of shoe inserts
Handmade wooden wedges by master Kurokio (Japan)
Wood types are used to make the blocks that are both stable, easy to nail, and do not change size significantly when exposed to moisture. Beech, hornbeam, birch, linden and maple meet all these requirements.
Master Kurokio doesn't say what wood he used, but it could be one of these types of wood.
Kurokio does not comment on his video lesson, but we will try to understand step by step how to make hooves for shoes by hand.
1 First, To make a pair of wooden shoe lasts you will need two pieces of wood, preferably square, about 15 x 15 cm.centimeter. Again, you need to know what type of shoe block you want to make - on a cobbler's shoe, the neck should be about 3cm higher than the top of the shoe. cm higher compared to a shoe block. Example. in the case of the shoe block, the original wood cross section may have been smaller, e.g. 12×12please refer.
How to make a shoe block at home
Once everything is prepared and the measurements have been taken, you can get to work. The plan is quite simple, just follow the instructions below.
- Put a bag or sock over your foot and start taping it. Stick with tape in one color.
- Cover the entire foot with tape of a different color. This will ensure there are no gaps. Repeat this process several times..
- Now Cut a piece Tape off along the front line. Be careful not to damage the leg. Repeat this process twice, on the left and right sides.
- Fill the resulting cavities with newspaper or mounting foam to give it rigidity.
- After filling Seal the cut out area with tape. If required Apply tape and foam to the inside of the workpiece. This way you can get the right size inserts for every type of job.
If the final size does not fit your foot, you can adjust it. Carefully trim the edges or add material if necessary.
If you've done everything right, you should have a great pair of insoles. You can use them to edit your shoes in any way you want. You can also make homemade slippers out of them if you want.
#4
OFFLINE LeLab
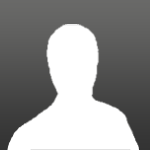

- From:Moscow
Dear colleagues!!!
Thank you very much. If I have any questions, I will ask them.
Best regards,
Andrey.
#5
OFFLINE yaso73











- Gender Male
- City: Novosibirsk
- Interests: I really enjoy living and don't like it when I'm hindered.
- From: Novosibirsk
All comments and moralizing are purely humorous.in no way violate the honor and dignity of the interlocutor shabby cat from the chimney.
Those who help people are wasting their time.
Prefabricated hooves and custom-made ones
While commercially available shoes are sewn onto pre-made lasts, custom shoes are made on lasts made to the dimensions of the customer's feet. Bernhard Rötzel, author of The Gentleman's Encyclopaedia of Men's Style, points out that 'it is the made-to-measure lasts that distinguish made-to-measure shoes from factory-made ready-made shoes'. He adds that 'the insole on which the shoes are made in the factory can only meet average criteria, although it is possible that they are very close. Church's, for example, produces up to six fullness options per model, and most men will find one of these completely satisfactory.'
What do the shoe lasts look like?
Shoe lasts differ in both shape and width ('fullness'). There are very elegant variants, there are more conservative variants and there are so-called 'fullness' variants. Country insoles used for country style models - and sometimes slightly larger than usual, as such shoes are intended to be worn with thicker socks than those worn with rough oxford shoes.
As for fullness, there are at least four types of insoles: E (narrow), F (standard), G (wide), H (extra wide). However, some American companies offer even more variants - up to nine (from extremely narrow AAA to very wide EEE).
Marked shoe lasts in standard size F'.
Rubber boots can also be classified according to the shape of the toes. There are strips with square, pointed, rounded toes and pointed toes with a straight front edge. The first two are hard to recommend, but the rounded toe is a timeless classic. The degree of taper and shape may vary. As Michael Anton noted, a rounded toe looks particularly good when the inside edge is almost parallel to the foot and the outside edge is slanted.
Shoes with a rounded toe
A peep toe with a more or less straight leading edge is less conservative than a rounded toe, but can look very elegant and sophisticated. In contrast to very square or very pointed toes, such toes can be found on classic shoes and boots.
Boot lasts with a narrow toe.
Last pattern of shoes
The hooves of shoes depend on the shape and size of the forefoot, that is, on the shape and height of the heel.
The variations in shoe lasts arise from changing shoe fashions and are determined by the general direction of garment modeling.
Depending on the shape of the hoof, the toe can be wide or narrow, blunt or pointed, oval or convex, elongated or blunt, high or low.
Trailing wedge hooves are used in externally shaped footwear. With these hooves, the upper, removable part (wedge) is held in the crest of the hoof block by a spring-loaded clip. The advantage of this last is its rigidity, which makes it easier to mold the upper and glue the sole on. Removing the wedge before removing the shoe from the hoof largely prevents the blanks from tearing out and significant deformation of the shoe*.
Articulated lasts are used for outer and sometimes inner shoes. Articulated lasts have the advantage over other lasts in that the shoe can be removed from the shoe without deformation.
can be removed from the shoe without deformation.
Slipper hooves (Figure 20)
are used in the shaping of inner shoes. Depending on the version, sliding strips can have an increased length of 9-16 mm.
Double lasts are used in the production of sandals and reversible shoes as well as in the production of slippers.
APPLICATION OF LASTS
Technical requirements for shoe lasts
Waffle hooves may deviate from the shape by up to 1 mm7 in width by 0.5 mm. The volumetric dimensions allow deviations of 0.55L, 0.72L and ti.68L to 2L.
When checking the blocks using the fit and cross-section templates, the following deviations are allowed: 0.5 mm less on each side in the cross-section and 0.5 mm less in the longitudinal section at the top, at individual points and at the bottom along the track.
The right blocks of the same type, size and fullness must be a mirror image of the left blocks.
The cleats must be free of cracks, rot, wormholes, knots at the wedge line and the plate attachment at the toe and heel as well as in the grip area along the trailing edge in the case of buckle and adhesive attachment. The metal plates should be firmly connected to the rails of the shoe and the wedge should be firmly connected to the shoe body^.
The corner dowels must be flush with the metal. shtick. The wood of finished wedges must not contain more than 8±2 % moisture, otherwise the wedges will dry out, change dimensions and crack during use.
Methods for checking wedges. The dimensions and shape of the wedges should be checked using control points. The control points are in the form of notches for wooden wedges and in the form of 'lanterns' for polyethylene wedges.
Notches or 'beacons' to control the size of the extensions should be placed in the following locations:
on the heel – on the side part, two punctures on each side near the back part of the heel in sections 0.G7L and 0.18L;
at the heel - on the back of the shoe at a distance of 0.551h, tracing this measurement along the axis of the footprint and drawing a line perpendicular to the intersection with the longitudinal axial profile of the back;
In the beam section, the top point is on the ridge at a distance of 0.72L', which sets the dimension along the foot axis and rises perpendicular to the intersection with the ridge profile, the lower points are on the foot edge at a distance of D .68L, which sets the dimension along the pivoting of the shoe along the axis. The puncture points on the heel are used to check the shape of the heel area of the shoe, on the heel and beam areas to check the size of the circumference (with an elastic band).
The height of the heel from the support surface is measured vertically with a metal protractor at the point where the back of the heel is rounded along the axis.
The performance of the cleats is determined by a multiple* of the refraction. The fitting must withstand at least 600 refraction cycles.
Influence of the hooves on the quality of the shoe. The condition of the hooves has a significant impact on the quality of the shoes produced. The following causes can lead to a deterioration in shoe quality:
– Fluctuations in hoof size.
Beyond what is permitted by the standard;
– discrepancy between right and left shoe,
the right shoe does not fit the left shoe;
– Shrinking of hooves with high humidity in low humidity environments
Drying out of high humidity environments and absorption of moisture by thinner hooves, causing swelling and dimensional changes
– Poor treatment (deburring) of the metal plates on the heel and toe.
Scarred (deburred) metal inserts on the eaves and throughout the hoof anvil, which can lead to damage to the lining and upper leather;
– A loose hoof wedge and an incorrectly aligned shoe sole.
Wooden or plastic plugs that are not flush with the metal plate; and misalignment of the components of the connected hoof;
– the production of untested and untreated bales
hoof blocks that have not been processed or repaired
– The use of pads that have defects (tri-.
It is recommended to have the shoes repaired by the manufacturer (maintenance and repair).
Care, storage and repair of shoes. Shoe sticks require special care.
The sticks should be stored in heated, dry rooms at a temperature of 16-20 *C and a relative humidity of 40-60%. Polyethylene wedges should be protected from direct sunlight. The blocks should be stored on special shelves with compartments for the different types, sizes and fillings. Care should be taken to store the stock in pairs. Inventory is checked at least quarterly. Unsuitable strips are removed from production and strips in need of repair are repaired. Unsuitable pads include those with a damaged hinge mechanism, pads with a cracked top disc, cracked or deformed toe and heel sections, cracked side surfaces, lost wedges and pads that do not meet dimensional standards.
Upholstery with punctured nails or bolts, partially chipped top pads, and partially damaged latches and tilt mechanisms should be repaired if possible.
Repair the chipped rails and top platform by gluing and nailing pieces of leather. The chipped parts of the rail should be hollowed out. A correspondingly large strip of hard tanning material is glued into the resulting groove and secured. The chipped part of the upholstery is knocked out and replaced with a piece of leather of the desired thickness. All parts of the leather that protrude above the surface of the upholstery are cut off with a knife and processed with a rasp.
We replace the joint mechanism and bushings with new ones or repair them.
Main causes of incorrect measurements:
– Incorrect measurement of foot and lower leg.
Incorrect measurement of foot, heel, ankle, shin, sole, arch and footprint;
– Inconsistency in the work of the person taking the measurement,
Incorrect hoof selection and fitting based on the client's foot and shin measurement;
– Changes in foot measurement due to movement throughout the day.
Fluctuations in measuring the foot throughout the day.
Correlation of foot length with shoe length. The basic dimension of the sealed insole is the foot length L, its width measured in sections 0.07, OD 8, 0.68, 0.90 and the circumference in the sloping section 0.55, 0.68/0.72 of the foot length from the top of the heel.
When determining the foot length L of the intermediate layers, a value of P=5 is added to the foot length. The following terms are used: b, shoe length; O, foot length; P, allowance for all shoe families and types, 10 mm, except summer shoes and shoes with oval insole, such as B. Moccasins, for which the allowance is 5 mm; 5, the offset of the footprint (insole) on the heel to the most protruding part.
The allowance P can be increased depending on the shape of the forefoot. For modeling shoes with narrow toes, the allowance can be 15-25 mm. This is because the toe area can only be tapered to the outside of the toe position.
Foot,
Series strips. A series refers to insoles of the same type but different sizes, associated with a certain pattern of changes in basic parameters. In mass production, shoes are produced in a limited number of fillings: everyday shoes, which are closed in three fillings with a circumferential distance of 0.72/G.68L – 8 MMt, model four fillings with a distance of 6 mm. The distance between adjacent fittings is e.g. B. 4 mm for casual shoes and 3 mm for elegant shoes,
There are 12 sizes (from 1 to 12). When moving from one shoe shaper to the next, one size fits all, the following information:
– Circumference in sections, mm 0.55L – & 0.72/0.68L – &.
– Sole width in sections, mm Q,18LH),7'0.8L -1.
Topography of the shoe hoof. The hooves of shoes have three different surfaces: the upper (called the instep), the lower or insole (called the footbed), and the lateral surface (located between the instep and the footbed). *>
A distinction is also made between the inside of the instep and the outside of the footbed. The upper, removable part of the shoe is called a wedge. The wedge is attached to the shoe using a spring fastener. The footprint of the shoe is divided into three parts: the rear, which rests on the heel, the middle, which rests on the heel, and the front, which rests on the toe.
The widest front part of the pad is called the bundle, the part that extends furthest inward is called the inner bundle, and the outer part is called the outer bundle. The convexity of the middle, central part of the pad is called the convexity and the uppermost part of the convexity is called the ridge.
Bale numbering system. Each shoe should be marked with the following symbols: size, fullness number and shoe index. The Shoe Index consists of five or more characters, each identifying a specific aspect of the shoe based on an agreed classification.
The first digit of the index indicates the purpose of the shoe by age and gender, which is made on a specific shoe last: boots - 0, hussars - 1, infants - 2, children - 3, school shoes for girls - 4, girls - 5, School shoes for boys – b, boys ^ 7, woman ~ 8t man – 9. ' ' ¦
The second digit of the index determines the type of footwear: closed shoes (boots, low shoes, sneakers, sandals) *– 1; light shoes (sandals, sports shoes, slippers, travel shoes, stockings) – 2; open-toed summer shoes (shoes with open toes or heels) – 3; insulated shoes The third digit describes the height of the heel part of the shoe: The fourth digit (coefficient KJ) characterizes the shape of the toe part of the shoe and is determined by the ratio of the toe edge a to the width of the toe edge B in the section L, which is at a distance which corresponds to the length of the foot, calculated from the outermost point of the heel, ie K – a/B. At K = 0.25 the forefoot is wide (indicated by the number 1), at K – 0.251. 0.549 – medium wide (Figure 2), with K = over 0.55 – narrow (Figure 3).
The fifth and subsequent digits indicate the sequential number of the shoe in the respective group. For example, a men's shoe with a heel height of 20 mm and a medium toe area is given the index 94224, where the last digit 4 indicates that there are three previously approved lasts in this group,
To give an example, let's decipher the last number 81233. The index numbers have the following meaning: 8 - women's, 1 - shoe, 2 - low heel (15-25 mm), 3 - narrow toe area, 3 - there are two already approved models in this group of deposits.
The shoe hoof index is supplemented with the letter M, and the hoof index for people with initial and significant foot deformities (including the elderly) is supplemented with the letter P.
The evolution of the hoof: How technology has changed over the last hundred years
A hundred years ago, hoof technology for shoes was very different than it is today. The craftsman at that time had to design the shoe on paper and make a model that was comfortable and practical for the wearer. The craftsmen of that time were guided by deep knowledge and a wealth of experience. Of course, there weren't as many models back then as there are today, but that doesn't detract from the complexity of making a shoe.
Today, drawings and hand carvings in wood have been replaced by computer-aided design. Special programs make it possible to design any style and shape of wedges without much effort. The design relies on statistically averaged data, making it possible to design a shoe that suits the vast majority of shoe buyers. The materials have also changed: from wood to plastic or metal.
An anecdote from a shoemaker. The Italian shoemakers say: 'No matter what we do, we make Italian shoes! Our cobblers say: 'It doesn't matter how, as long as it's like the Italian'. It is worth noting that domestic shoes have recently increased in quality.
What are good lasts for shoes useful for?
Undoubtedly, lasts play a crucial role in the comfort of shoes. For example, if the height of the shoe is too high when the raw material is cut and the insole is too narrow, a tight shoe is guaranteed. So the fit of the shoe determines how comfortable the shoe will be. Experienced shoemakers say that 8 out of 10 women should judge a pair by the last.
The lasts are designed for specific shoe models, boots or sneakers. The heel height is also not insignificant. As you can see, the number of lasts and their role in creating high-quality and comfortable shoes are undisputed.
–Keywords
- Knitted bows, hair clips, hoops and other jewelry (57)
- Knitting patterns, embroidery patterns (4)
- Paper dolls (4)
- Knitting for children (128)
- Women knit (151)
- Home design comfort (4)
- Dollhouses, furniture (76)
- Rabbits and kittens (79)
- Sock and Glove Toys (43)
- crocheted toys (186)
- Needle toys (83)
- Dolls (599)
- Raeburn dolls (2)
- Peacock and MK's dolls (21)
- Lydia Calambet dolls (79)
- Master class by Elena Lavrentieva (26)
- Things to do at home (278)
- Microphone from LIKMA (18)
- my works (8)
- Plush toys (278)
- Reconstruction of old objects (48)
- Shoes, socks, boots (134)
- Quilts, sleeping bags, blankets etc. (84)
- original gifts, bouquets, etc. (8)
- Songs and stories (2)
- Crafts from plastic bottles (26)
- Hairstyles (9)
- Educational games for children (111)
- Recipes (145)
- Handmade (everything and nothing) (145)
- Bags (36)
- Knitting and crochet programs (2)
- Sewing for the whole family (81)
Making insoles for shoes.MK
Link to Milena's website (http://milena.vitalory.ru/masterskaya,32.html) Materials required:
- Adhesive tape – for making the molds for pouring
- Fabric (e.g. food-safe plastic) – to create a base for the molds
(alternatively, instead of tape and foil, silicone sealant + vegetable oil and a plastic knife/spatula)
- Plaster – used to make (mold) the shoe itself
- Sticks (wooden or plastic) – to help grip the shoe (something else can also be used).
- Scissors (knife) – material to be used
- Colored pencil (marker) – for marking
- Glue – to attach the sole and handle
- Adhesive tape (paper) – used to make the sole
- Cardboard – to form the sole
- Water putty – for customizing the shoe
- Abrasive sand (emery paper or loose sheets) – for the finish
- Wood filler (or acrylic paint) – to cover the finished shoe so it doesn’t get dirty.
- Varnish – for applying the final coat.
- Aids – cloths, plaster mixing board, tray, etc.
Unattainable ideals
'I fell in love with my job. I think that came with the realization that my work was needed and liked by the people I worked with. The hardest part is creating a base that the designer likes. When working with a designer it is important to understand what they want but also that it is both beautiful and functional. This is of course very difficult and sometimes there are contradictory situations, especially if you start from a prototype and not a sketch. The designer must not only be an excellent artist, but also a shoe designer who knows exactly what the shoes are intended for. Because what's the point if the shoes are beautiful but uncomfortable? My master, who I studied with, always said: You can make bad shoes on a good sole, but you can't make good shoes on a bad sole. A shoe is like the foundation of a house: if the foundation is faulty, sooner or later it will crack, collapse or fall apart. In our industry you can't make mistakes, but you can't do everything perfectly either, because the sole of a shoe has to fit as many people as possible. So there's no perfect pad, and I don't have a pad that I'm proud of - I just don't think it's something to be proud of. Even when I finish a pad and am happy with it, I still notice flaws after a while. Of course you can turn a blind eye, but we have been taught otherwise. Sometimes it even happens that I finish a job and the next day I look at the paper, throw it away and start again. The shoemaker is not obliged to design a radically new shape, he has a different task - to make a shoe that will sell in Russia, that will be comfortable and made in the same style - that is what the designers demand. And there is nothing new to invent - everything has been invented before us. Shoe factories keep a copy of each shoe model, and with such collections you get the impression that everything has been done before. Even in the pictures of empresses and noblewomen you can see that the heels, the shape of the toes, the heel - everything is the same as ours, and the circle is complete. Only time and our perspective change. The shoe also remains the same because it does not come into being on its own, but is created on the basis of its predecessors. There are standards developed by craftsmen and the shoe is not made from scratch every time. The shoemaker glues or welds new elements onto the existing insole, taking into account the positive qualities of the original and making it the way the designer likes it or how it will sell better. The result is a larger deposit. However, since my school is based on working with wood, I use the more-to-little method - I cut off the excess from the shoe. That's my way of working and I always just use my pads, correct the negative and keep the positive.'
Work with pads, pay with pads
'I worked in the fashion house for 10 years, and then it was moved by Sadov-Triumfalna to a new building in Cheremushki. There was a factory there that the ministry decided to make experimental and hand over completely to the fashion house. This was the right decision: it is one thing to make upholstery and not enter the production process, and another to communicate with the technologists and understand what is profitable to produce and what is not. But by that time we had already had some disagreements in the House of Models, and it was a long drive to Novye Cheremushki. Anyway, I don't remember exactly how, but I was lured to the Day Services House in Chimki, which belonged to the Ministry of Day Services. They also had their design offices there, only they were not intended for industry but for private studios. I worked there for six months and realized I had made a mistake. It wasn't even about the people, because almost all of the House of Models employees moved there with me. I just realized that it wasn't for me: other tasks, not so interesting. But I didn't want to go back, I thought it wouldn't be good. Because I needed a job - I already had a family at that time - I got a job as a wheelwright in the First Model Factory in Krasna Prešeni. I worked for two years and then I was invited to Cuba's shoe factory. Previously, ordinary slippers were produced there, but when a very strong model-designer, Dawid Lvovich Zabryansky, came there from the fashion house, the factory began producing moccasins and became an interesting experimental production. In total, I worked at Kubinka for 15 years, but every five years I quit because there wasn't enough work. But every time I was called back, I came back because it was interesting to work there. On my second trip to Italy, I met the director of the Armavir shoe factory, Gennady Arkadyevich Shupletsov, in our delegation. Shortly after perestroika began, he and I decided to start our own company to make coasters. I designed the coasters and the factory in Armavir manufactured them. By that time, I was already known throughout the Soviet Union's shoe industry, and Moscow shoe designers were able to participate in the company. Everything was very interesting until we had to pay our workers with barter due to the shortage in the country. And how should wages be paid in blocks? Who needs that anyway? So I closed the company and started working for those who knew me and invited me to work. I worked for Liski's company for 10 years, and then I went to China for the first time. Now I work for Spark, and this Spring/Summer 2014 collection is my first for the company. Actually, I don't like changing jobs because I have to organize my workspace so that I can do what I need to do, regardless of external circumstances. Now I work mainly in China, and everything there depends only on me. If I do a job badly, it is entirely my fault. In Russia you can leave the customer in the lurch in terms of deadlines because not much depends on you: if I design the last of a shoe here, I can't immediately sew it and check my work, while in China there are all the possibilities. I would like to work again with the people who make fashion, with the people behind the industry. My gut feeling tells me I could do this. You know what they say: It doesn't matter how old you are, but how you feel. I feel young, absolutely young. And on all my business trips I try to come into contact with young people. It's true that I stand out from them, but let them think what they want. I will communicate with young people, because young people are life.
Read more:- insoles for shoes.
- Manufacture of shoe lasts.
- The insole of your shoes falls off.
- Manufacture of soles for shoes.
- Manufacture of shoe inserts.
- rim on the shoe.
- Equipment for manufacturing orthopedic insoles.
- Shoes fall off the heel - what to do?.