1.5. The soles are made of genuine leather or shoe board, which is made of regenerated (cut) genuine leather, which allows the use of tanning waste. The regenerated leather can be easily disposed of later without polluting the environment.
- KÖTL – manufacturer of brake pads
- ecology
- #2 OFFLINE Trofimych
- #3 OFFLINE Znachor
- tools
- Work with the materials you have
- Making shoes from doll blocks with your own hands
- Step by step and in detail
- Stage 4: assembly production.
- design features
- materials and tools
- sewing machines
- sewing machines
- Step one (and the most important). Creating the last
- Second step. Designing a future pair of shoes
- How much money does it take to open a 3D printer to make insoles and shoes?
- How much money can you make by opening a shoe manufacturing facility with a 3D printer?
- Assembly
- Print the heat markers
KÖTL – manufacturer of brake pads
KÖTL is a Russian manufacturer of brake pads for cars and vans.
The company's roots date back to 2011, when a group of European investors with significant assets in the automotive aftermarket opened a cluster of manufacturing facilities in Russia. It started with a plant for the production of friction pads for disc brakes in Tver.
The automotive industry of the world's leading automotive companies such as Volkswagen, Ford, Toyota, GM, Nissan, etc. was actively developing in Russia. Both had a program to localize component production due to government regulations and naturally had an interest in Russia becoming a world-class automotive supplier.
The design of the production facility and the commissioning of its planned capacity was carried out by leading European technologists with more than 30 years of experience in order to ensure the highest level of braking properties and consumers from the very beginning.
In 2012, the production of brake pads was started at the KÖTL plant in Tver:
- A supply chain management business process has been implemented;
- The product quality has been evaluated according to the international requirements and standards;
- Custom production for European customers from the automotive industry was organized.
2014 – Reorganization of the investor structure:
- The plant was completely taken over by Russian investors;
- The plant falls under the import substitution program of the Russian Ministry of Industry;
- Control of production, compliance with technology and product quality by European employees and technologists;
- Maintaining long-term contracts with European partners and identifying further cooperation opportunities.
ecology
We strive to minimize the impact of our operations on the environment and human health by:
#2
OFFLINE Trofimych
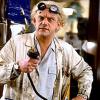





- Gender Male
- From:Ekaterinburg
Basically, a machine with a rotary axis should suit your needs. For the right information about the characteristics of the machines – give what are the maximum dimensions of the shims.
#3
OFFLINE Znachor
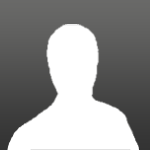



- Gender Male
- City: Vilnius-Murcia
- Interests: very interesting interests
- From:world
If there are no undercuts - it can be done without a torsion axis.
And as much as possible - you can use a Chinese 'hobby' for torsion, no need to catch hundreds.
tools
Work with the materials you have
These materials and tools are required for crafting Shoes with buckles for the doll.
These are the basics. If you don't have any of these things, that's no problem. They can all be replaced and put together.
For example, if you don't have foam for the sole, you can replace it with pieces of leather, or you can even forgo it and make a single-layer sole.
If you do not have a microporous wound for the sole, replace it with another suitable material (thick leather, foam).
You can eliminate the blocks and assembly tools by making small holes for the laces with an awl and replacing the laces with thin satin ribbon or twine.
Making shoes from doll blocks with your own hands
Step by step and in detail
All materials are ready. Let's start making Shoes for rag dolls.
The pattern is being transferred straight to the last blocks of paper and the wrong side of the leather.
The leather blanks should be cut out and soaked in hot water for about ten minutes to thoroughly soak them. This is a necessary condition. Otherwise the leather cannot be stretched and will not take the shape of the upholstery.
I have, among other things, several cushions for doll shoes. for doll shoes.. That's why I make several pairs of shoes at the same time. That saves time. In the picture on the right you can see the white leather part (I just forgot to take a picture of the blue one).
The wet part must be stretched well over the shoe block and secured with safety pins.
At this point you need to use a pad. It's a good idea if you have a cork pad that is used in the kitchen for hot pans (such pads are available from Ikea).
Since I don't have one at the moment (I took it to the country), I use soft cardboard in several layers. It absorbs excess moisture very well, which speeds up the drying process of the items.
I put the pads with the wet leather in as warm a place as possible until they are completely dry. This sometimes takes up to 24 hours. I'm waiting, but I'm not wasting my time - I'm making the semi-finished parts, ie the accessories for the new dolls.
Stage 4: assembly production.
At R-CLASS, the top dolls are assembled exclusively by hand.
This process is labor intensive but ensures high quality assembly. Each lace master has a mark that he puts on the sole of the pointe shoes, which guarantees the master's personal responsibility for the quality of the assembly.
The assembly of pointe shoes consists of a large number of work steps. The photo shows a small part of these processes.
design features
In today's market there are a large number of models of shoes that differ in material and design. Before delving into the production steps of leather or suede products, it makes sense to familiarize yourself with the construction, the components and their differences.
The components that make up the upper of a shoe:
- The sock is the part that covers the surface of the toes and protects the foot from mechanical damage, mostly caused by contact with the external environment.
- The sock is the part that covers the back of the foot. It is subjected to constant bending when walking and therefore deforms first.
- Ankle shoes cover the lower part of the shin and ankle. This part is practically not affected by external factors during wear.
- Eyelets - a place where laces and cables attach.
- Cuff - the part that closes the heel part of the foot.
- Tongue – the part attached to the base of the shoe that fixes the foot and prevents dust, dirt and small elements from getting inside.
- The insole is a layer of soft and comfortable leather (or other material) that is in direct contact with the foot, cushioning walking and eliminating discomfort even when running.
The lower part of the shoe consists of the following elements:
- The sole is the most important part of the outsole, which not only decides the walking comfort but also the durability of the product. It protects the foot from unpleasant ground contact and absorbs mechanical shock when jumping, running and walking.
- The heel counter is the part that lifts the heel of the foot. It can come in different shapes and sizes depending on the model and seasonal design.
- Heel Pad - attached to the surface of the heel to protect it from abrasion.
- Rim - a detail responsible for fastening the bottom of the shoe.
- Protective inserts - elements made of cotton fabric and polyurethane that prevent chafing and blisters on the heel.
- Padding - Material that provides breathability, warmth, ventilation and protection from seasonal weather conditions.
- Insole – the part that is placed between the sole and the base of the insole creates the necessary rigidity and flexibility.
materials and tools
Before making shoes with your own hands, it is important to choose the right material and get the right tools. Products for adults or children are most often made of leather, suede and textiles. Shoes made of natural leather are popular because they are durable, practical and durable, and the risk of foot abrasion is significantly reduced. Sneakers, boots, boots, sneakers, sneakers, flip-flops are made from this material.
Suede is a comfortable, soft and flexible material used for both adult and children's shoes. It has no top layer, is labor intensive to manufacture and therefore quite expensive. Fabric - used for sewing summer shoes, children's shoes, sneakers, and also slippers. The material is very soft, delicate and pleasant to the touch. In such shoes, the foot is always breathable, receives the necessary ventilation, comfort and warmth.
Textiles are environmentally friendly, which is why they are most often used for children's shoes.
When making the sole with our own hands, we use leather:
- Leather - it is very resistant, durable, protects the foot from external damage and allows it to breathe. Leather soles are as easy to make with your own hands as any other material.
- Rubber – an abrasion-resistant material, resistant to frost and temperature changes, and has thermoplastic properties. It is distinguished by its strength, practicality and durability. The only drawback is the high marking of such soles.
- PVC is an inexpensive material that has good abrasion resistance and can be colored. It is used for winter shoes. The downside is that it's too heavy.
- TPE - made from thermoplastic rubber, has good abrasion resistance and does not slip on wet surfaces. Disadvantage: it is not possible to get a clear and smooth contour.
- Polyurethane - has low thermal conductivity, is soft, light and can be used for all seasonal models. Easy to fix. This material is widely used in the shoe industry. The disadvantage is that it is not very durable and wears out quickly.
sewing machines
shoe sewing machines are suitable for difficult materials such as leather, oilcloth, suede, rubber and canvas. The column type is considered the most versatile device, which is why it is most often used for shoe manufacture. The main task of a shoe sewing machine is to ensure easy material transport and high maneuverability of the seams.
The Geran lux (launched in 1998) can help with this technique. The selection is sufficient.
The ZOJE ZJ9620-BD-H-3/01, for example, is an analogue of the PFAFF.
It is a two-needle lockstitch machine with a direct, energy-saving drive (with built-in servomotor), with upper and lower shafts and synchronized needles and a swiveling needle bar. The Unisono feed system ensures stable fabric feed and good sewing quality. The pressure roller provides maneuverability when sewing circular stitches. The ZJ9620-BD-H-3/01 comes with an integrated remote control and built-in light and has step and stop buttons during operation.
sewing shuttle type. Stitch length up to 36 mm. Needle spacing of 1.8 mm and 2.4 mm.
sewing machines
The purchase of machines is a logical consequence of increasing the production volume. In addition to sewing machines for various purposes, the company 'Gueran lux' offers modern and powerful sewing machines.
ORIGINAL OE-5770B-6040 - automatic sewing machine with programmable stitch, pendulum stitch, sewing field 600h400 mm, with direct drive.
The machine is designed to perform many programmable stitches in products made of various types of materials, from medium to heavy. Used for decorative finishing of handbags, shoes, sewing scarves. Ideal for assembling shoe parts.
The ORIGINAL OE-5770B-6040 has automatic functions: thread trimming, locking, sewing foot lift, needle position adjustment and thread breakage detection. The machine has automatic pattern recognition and can recognize up to 30 patterns at the same time.
The ORIGINAL OE-5770B-6040 is equipped with a pneumatic, two-stage clamping system.
The OE-5770B-6040 is based on a BROTHER machine.
Energy efficient 1kW motor. Requires an air pressure connection of 0.5 MPa, 1.8 l/min.
Step one (and the most important). Creating the last
A shoe last is a special device used to give the shoe the right shape and to keep it in place during production. In other words: He is the foundation of the future couple, the most important part! It determines how the shoe will ultimately look and whether it will be comfortable for the wearer. You've probably heard the expression 'comfortable fit' more than once, right? This fact often determines whether or not you decide to buy a particular pair in a shoe shop!
The cut can be for both men and women. Also, every shoe is made in a standard size – 35, 36, 37 and so on.
By the way, there is even such a profession – shoemaker. It is quite rare, but extremely important in the shoe industry. And interestingly, he combines both creativity and mathematical precision!
Second step. Designing a future pair of shoes
Now the designer comes into play. He knows what the finished pair of shoes should look like and draws his sketch right on the last page. Then all the elements are worked out – tops, bottoms, decorations. The designer sees how the lines run and decides where the cutout needs to be moved a few millimeters, made wider or narrower.
How much money does it take to open a 3D printer to make insoles and shoes?
It takes about $8,000 to 3D print shoes at home. The main cost is the purchase of the printer. A good pair of Lewihe sneakers costs around $3,000. It can work with all operating systems, uses PLA filament, Filaflex with a diameter of 1.75mm and has a print speed of 150mm per second. An optional printer can be purchased over time. The Lewihe ProXL model costs twice as much (about 6,000 $) but has better specs and allows you to print a trainer in one session.
Opening a small orthopedic practice, according to the most conservative calculations, will cost about half a million rubles. Cost list:
- Obtaining a license and registering the company in the legal field: 60 thousand rubles.
- Repair and preparation of the premises: 250 thousand rubles.
- Purchase of raw materials (thermoplastics) and equipment: from 120 thousand rubles.
- Advertising: from 60 thousand rubles.
The production of leather shoes requires an initial investment of several million rubles. Production halls and an office for cooperation with customers have to be rented. Purchase of equipment can cost 1-2 million rubles. Raw materials must be purchased in square meters:
It is not profitable to open such a business from scratch in a small town. To make the business profitable, it can be set up in bigger cities like Moscow and St. Petersburg and work on demand, also with customers from Europe.
How much money can you make by opening a shoe manufacturing facility with a 3D printer?
Shoes printed with a 3D printer can be sold for 1,500 rubles. As a rule, such a company is aimed at making a profit on a large number of sales. For an additional fee it is possible to organize custom printing of shoes in the presence of the customer. With a good website it is possible to earn 120-150 thousand rubles net per month.
Information The cost of making an orthopedic insole, including measurement, is 4-5 thousand rubles. Additional income comes from the correction of orthoses, as well as from consulting a specialist in this field – an orthopedist. With the accumulation of customer bases, one can count on an income of 300-400 thousand rubles net per month.
High-quality leather shoes can be sold for 10 thousand rubles or more. When you work with retail chains, half of the profit has to be paid for the sale of your goods. This option is preferable only when there is a high demand for the products. For starters, you can try an online store that caters to each customer individually. Opening a shoe store with high-quality European shoes will provide you with a stable income of 300,000 rubles per month.
Assembly
After that, they just need to be assembled using dowels and PVA glue.
The WTO pad is ready for final assembly, the last two pieces just need to be put together with three pins.
Print the heat markers
And finally – the tastiest part. We stamp our logos with the heat press, I've written about that before.
Finally I would like to say, download the drawings and make your own stamps. After sewing friends who were able to judge them to make this archinuzhnuyu thing. Make such a pad yourself, it's not difficult. And if you can't make it yourself, write me in the comments - make it for you and send it to the transport company or by mail. The cost of the coasters themselves is in the region of 2500 rubles (depends on various reasons, primarily on the cost of purchasing lime, but does not vary too much), plus the cost of delivery, which varies and depends on the carrier on average from 300 to 500 rubles.
Recently there have been many requests for a drawing the size of two A4 sheets. They have been included in the archive, which can be downloaded at the beginning of the article.
Read more:- How Much Does an Orthopedic Surgeon Make?.
- Shoe manufacturing technology.
- Custom made shoes.
- make shoes.
- Production of women's shoes.
- Custom made orthopedic shoes.
- How much does it cost to sew a bespoke shoe?.
- Making hooves for shoes.